A Comprehensive Guide to Visual Inspection AI and Its Types: An Industry Insider's Perspective
What You Will Learn from This Article
What makes AI different from what has come before? There are various similar products on the market, but what are the differences? What are the key points when comparing and selecting them? You rarely find articles that honestly address these questions. Here, we will answer them frankly from a vendor’s perspective!
What is Visual Inspection AI?
Image Processing and AI
Until around 2016, traditional image inspection systems primarily relied on a technology called "image processing." However, recently, defect detection using AI has become more common. What are the differences, and what should you know before implementation? Let’s start by briefly reviewing these distinctions.
What is Image Processing?
What exactly is image processing? Let’s explain using a real-world example.
For instance, suppose you want to detect dirt defects on fabric, as shown in the image below. For this type of defect, the first step is to extract areas corresponding to the color of the dirt (displayed in white in the extracted area). However, since some parts with similar colors remain, noise reduction processing is applied. Despite this, parts unrelated to the actual defect still remain. In other words, this can cause over-detection.
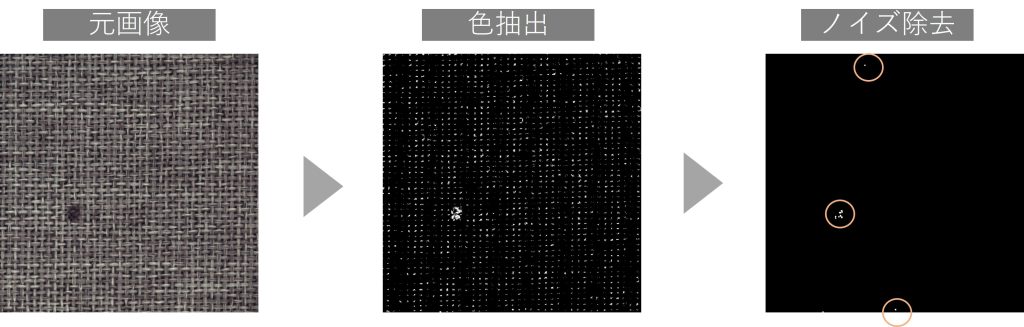
What is AI?
What exactly is AI? Recent AI, not only for visual inspection but generally, often refers to a technology called "deep learning." What does deep learning do in visual inspection?
Deep learning, modeled after complex neural circuits in the human brain, is also known as a neural network with a deep structure. For example, when looking at the image above, a person might intuitively sense, “This might be a defect.” The neural circuits that allow for this “intuition” are not as straightforward as image processing. However, this combination of complex processes allows for highly accurate defect extraction.
Deep learning enables this. For instance, you can input images into a neural network and feed it many datasets that mark the precise locations of defects, allowing it to “learn.” Through this, it automatically learns complex processes and can detect defects when given data during actual inspections. The ability to perform complex processes generally results in higher accuracy.
In fact, deep learning, particularly a structure known as a CNN (Convolutional Neural Network), has a structure similar to the receptive fields in human vision. Each layer in the neural network, learned through training, functions like an image processing filter, optimizing each layer through learning.
Please refer to this article as well.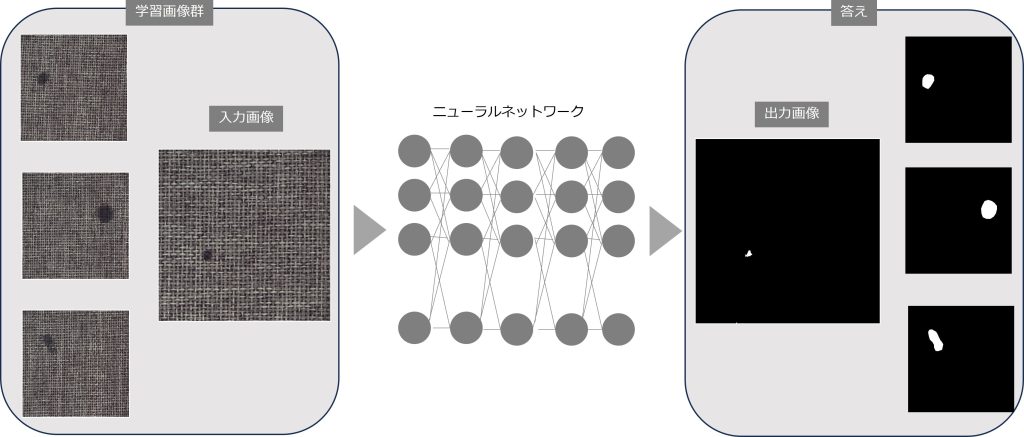
Summary of Differences Between Image Processing and AI
The content above is summarized in the table below.
Method | Definition | Advantages | Disadvantages |
---|---|---|---|
Image Processing | A process-based approach for defect detection. | It’s clear why a defect is detected based on the process settings. | Challenging to set detection for complex shapes; prone to over-detection. |
AI | Detects defects by learning features of defective and non-defective items. | Can be applied to complex products and is easier to set up with training. | Requires preparation of data for training, which can sometimes be labor-intensive. |
Types of AI in Visual Inspection
In the earlier explanation, we discussed an example where AI is provided with a dataset of defective images and their corresponding defect locations, but there are actually several output methods for AI. We will introduce the main methods used by various products. Note that the type of AI used may differ depending on the product.
Main Categories of AI
・Supervised Learning: Also known as defect learning. Defective data is fed to the AI. If well-trained, it can achieve high accuracy and even output defect types. However, in environments with few defects, collecting data for training can be burdensome. Additionally, it’s important to note that it cannot handle new defect types.
・Unsupervised Learning: Also called good product learning, anomaly detection, or anomaly detection. This approach involves training the AI on good products to detect anything that deviates from this pattern. Unlike supervised learning, where defects are explicitly taught, in unsupervised learning good products are gathered routinely, making it an attractive approach. It avoids the burden of collecting defective samples and can handle new, unknown defects.
Learning Method | Definition | Advantages | Disadvantages |
---|---|---|---|
Supervised Learning (Defective Item Learning) |
An approach where defective data is taught to the AI. | High accuracy when sufficient data is gathered. | Labor-intensive to gather defective data. May miss defect types not taught. |
Unsupervised Learning (Good Product Learning) |
An approach where AI learns what is considered good and detects anything that differs. | Good products are easily gathered and allow for quick inspection setup. | Cannot classify defects and often leads to over-detection. |
Subcategories of Supervised Learning
When choosing a product, it’s essential to consider the AI type and its characteristics carefully. The process of teaching defects to AI is commonly referred to as annotation, so we will use this term going forward.
・Classification: In classification (also called categorization), defective data is taught to the AI without specifying defect locations. This method simplifies the work for data collectors since they don’t need to specify the exact defect location. However, AI lacks valuable hints on defect characteristics, which can make it less accurate.
・Object Detection: Within defect learning, object detection allows you to output defect areas as rectangles. This method requires defect location data, meaning annotation is more labor-intensive. However, it’s more accurate than classification and makes it easy for humans to understand the AI’s judgment due to visible defect locations.
・Segmentation: In segmentation, defect areas are indicated in freeform shapes, allowing precise defect area output. Although annotation is labor-intensive, it provides more detailed defect analysis.
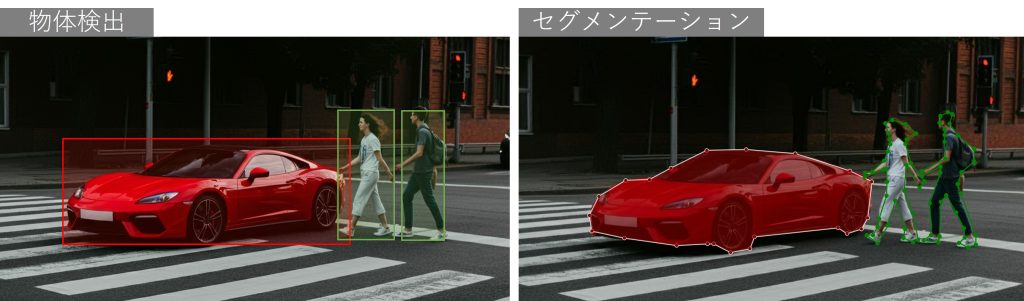
Regarding supervised learning, a summary table is provided below. From the author’s perspective, segmentation is the most recommended method. In on-site inspection, the main challenges involve collecting initial data for annotation and frequent human intervention due to over-detection. Segmentation improves human interpretability of AI's judgment and simplifies inspection customization, reducing the need for human intervention.
Output Method | Definition | Advantages | Disadvantages |
---|---|---|---|
Classification | Classification of data into categories without specifying the defect location. | Low annotation burden. | Accuracy may be low. |
Object Detection | Allows defect detection as rectangles. | More accurate, easy to understand AI’s judgments. | Requires a moderate amount of annotation. |
Segmentation | Output defect areas as freeform shapes. | Highly accurate. | High annotation burden. |
Thank you for reading to the end. We hope this article has been helpful!